
Cementitious Materials Developing and testing cementitious materials solutions for the future.
Cement and Concrete Research
With a vast array of testing equipment and decades of scientific expertise at our disposal, UK CAER’s cementitious materials scientists explore methods for improving the compositions of cement and concrete samples through various characterization and testing methods.
Belite-based Cements
CAER and project partners have created a rapid research-to-product approach with the commercial development of a novel, extremely durable concrete product based on low-carbon, low-energy belite-rich similar to ordinary portland cements. These materials create less carbon dioxide, require less energy during manufacturing, and lengthen the life of concrete.
Coal Combustion By-Products
We’re developing novel technologies and processes for transforming fly ash from coal-fired power plants into renewable products and materials.
Using Recycled Materials to Develop an Energy-Efficient Alternative to Portland Cement
Portland cement is the most common type of cement in general use around the world as a basic ingredient of concrete, mortar, stucco, and non-specialty grout. The low cost and widespread availability of the limestone, shales, and other naturally-occurring materials used in Portland cement make it one of the lowest-cost materials widely used over the last century. However, Portland cement also presents serious health and environmental concerns. A caustic material, Portland cement can cause chemical burns. The powder can cause irritation or, with severe exposure, lung cancer, and can contain some hazardous components, such as crystalline silica and hexavalent chromium. Environmental concerns are the high energy consumption required to mine, manufacture, and transport the cement, and the related air pollution, including the release of greenhouse gases. At UK CAER, our researchers are addressing this challenge by exploring methods for using fly-ash, a by-product of coal combustion, as a more energy efficient alternative to Portland cement.
Creating More Environmentally Friendly, Stronger Cement
CAER has received a two-year, $1.3 million grant to develop extremely durable belite-based cement — an alternative to ordinary Portland cement — that is low-energy consuming and low-carbon dioxide releasing. The project, titled “Belite Cement, and Concretes; Novel Low-Energy Approaches to Making Concrete Extremely Durable,” is funded by the U.S. Department of Energy Advanced Research Projects Agency–Energy (ARPA-E).
New Concrete for Damaged Structures
Imagine a tragedy where an act of terror damages a building, runway, tunnel, bridge or dam. Now imagine a quick-curing concrete that can be sprayed to reinforce the structure almost immediately, before it fails catastrophically, providing safety for rescue workers, who risk their lives minutes after disasters hit. A technology developed at the University of Kentucky Center for Applied Energy Research (CAER) and Minova North America headquartered in Georgetown, Ky., does just that. The products, called Tekcrete Fast and Tekcrete Fast M (with a specific application for mining safety), have been licensed by Minova, and can be used by engineers to immediately stabilize damaged structures. It is a high-strength, quick-setting concrete that achieves set and structural strength in minutes. Minova has licensed the technology for application in the underground mining, civil and tunneling industries as well. Read the Full Story
Establishing Quality Assessment Guidelines for Coal-Combustion By-Products
The closing of hundreds of coal-fired power plants across the United States, compounded with the increased use of additives for acid gas and mercury control, is resulting in a new economic dynamic for the high-quality fly ash used in cement and concrete applications. As the number of sources for high quality coal ash continue to dwindle, many are concerned over future supply constraints. UK CAER scientists and engineers serve as global thought leaders, developing industrial guidelines for the proper use and storage of fly ash as a raw material for cement and concrete products.
Our cementitious team is recognized globally for their work in organizing the World of Coal Ash Conference. WOCA is an international conference organized by the American Coal Ash Association (ACAA) and the University of Kentucky Center for Applied Energy Research (CAER). The 2024 conference in Grand Rapids, Michigan will be the 10th joint biennial meeting with a focus on the science, applications and sustainability of worldwide coal combustion products (CCPs) as well as gasification products.
Visit worldofcoalash.org for more information
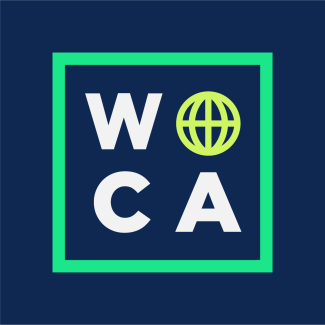
Featured Publications
T. Robl, A. Oberlink, R. Jones, “Coal Combustion Products (CCP’s) Characteristics, Utilization and Beneficiation”, Woodhead Publishing, 1st Edition, 2017.
T. Y. Duvallet, L. Frouin, T. L. Robl, A. E. Oberlink, and R. B. Jewell, “Effect of Particle Packing and Fly Ash on Performance of Ordinary Portland Cement/Anhydrite-Activated Ground- Granulated Blast-Furnace Slag”, ACI Materials Journal, 2017, Vol. 114, Issue 4, 653-660.
T. Duvallet, Y. Zhou, K. R. Henke, T. L. Robl, R. Andrews, “Effects of ferrite concentration on synthesis, hydration and mechanical properties of alite-calcium sulfoaluminate-ferrite cements”, Journal of Sustainable Cement-Based Materials, 2017, Vol. 6, Issue 2, 85-110.
P. Mills, T. Robl, R. Rathbone, R. Jewell, “Cementitious Compositions”, U.S. Patent Number 9,284,226 B2, issued on 03/15/2016.
R. B. Jewell, K. C. Mahboub, T. L. Robl, A. C. Bathke, “Interfacial Bond between Reinforcing Fibers and Calcium Sulfoaluminate Cements: Fiber Pullout Characteristics” ACI Materials Journal, 2015, Vol. 112, No. 1, 39-48.
A. Oberlink, R. Jewell, “Rapidly Deployable Shotcrete System”, Shotcrete Magazine, 2015, Vol. 17, N. 4.
T. Robl, T. Duvallet, R. Rathbone, Y. Zhou, “Hybrid cement clinker and cement made from that clinker”, U.S. Patent Number 8,986,444, issued on 03/24/2015.
R. Hill, R. Rathbone, J. C. Hower, “Investigation of fly ash carbon by thermal analysis and optical microscopy”, Cement and Concrete Research, 1998, 28(10), 1479-1488.